Why do we use a more complex, more expensive from the consumables ago welding technology? Because we do not see any sense in "beautifying" high quality stainless steel or aluminium with corroding welds...
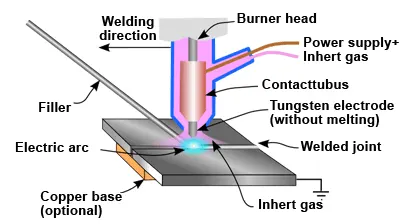
Why do we use the TIG-welding technic?
The tungsten inert gas welding (TIG welding process) comes from the USA and was known there in 1936 under the name Argonarc welding. After the 2nd World War it was introduced in Germany. In English-speaking countries, the process is called TIG after the English word "Tungsten" for tungsten. The process is distinguished from other fusion welding processes by a number of interesting advantages. It is e.g. universally applicable: if a metallic material is even suitable for fusion welding, then it can be added with this method. On the other hand, it is a very "clean" process that generates hardly any spatters and only a few pollutants and, when used correctly, ensures a high-quality welded joint. A particular advantage of TIG welding is that the addition of welding filler and the current intensity are decoupled here compared with other processes which work with a consumable electrode. The welder can therefore tune his power optimally to the welding task and only add as much welding filler as is currently required. This makes the method particularly suitable for welding root passes and for welding in predicaments. The advantages mentioned have led to the method being particularly well suited for welding aerospace equipment, components of nuclear technology, for the construction of chemical plants and equipment as well as of course for high-quality work by us on your vehicle and its parts.
Made to measure In the TIG process
The advantage of freedom from rust makes the TIG welding process, whether in aluminium or stainless-steel welding work, the first and only choice. With the TIG technology and our know-how it is easy to manufacture something like an intercooler for an Ascona C. The customer's demand was that the original appearance of the Ascona should not be falsified by an intercooler hanging under the apron.
In such everyday work as the production of charge air ducts, trouser pipes, downpipes, baffles in and on the body, etc., of course, the TIG process also comes into play.
Another advantage of our way of working is the fact that we build a welding gauge for custom-made products (such as for the front of a Bora 1.8T in the picture below) so that we can reproduce the part without having the vehicle in house.
It is best to convince yourself of our welding skills and to understand why customers from all over Germany and neighboring European countries come to us. Interested? Then you are welcome to contact us.
Why do we use a more complex, more expensive from the consumables ago welding technology? Because we do not see any sense in "beautifying" high quality stainless steel or aluminium with...
read more » Close window TIG-welding FAQ
Why do we use a more complex, more expensive from the consumables ago welding technology? Because we do not see any sense in "beautifying" high quality stainless steel or aluminium with corroding welds...
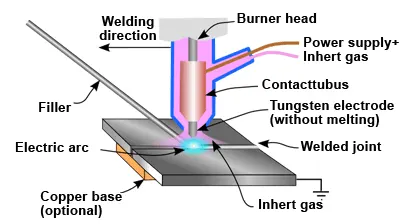
Why do we use the TIG-welding technic?
The tungsten inert gas welding (TIG welding process) comes from the USA and was known there in 1936 under the name Argonarc welding. After the 2nd World War it was introduced in Germany. In English-speaking countries, the process is called TIG after the English word "Tungsten" for tungsten. The process is distinguished from other fusion welding processes by a number of interesting advantages. It is e.g. universally applicable: if a metallic material is even suitable for fusion welding, then it can be added with this method. On the other hand, it is a very "clean" process that generates hardly any spatters and only a few pollutants and, when used correctly, ensures a high-quality welded joint. A particular advantage of TIG welding is that the addition of welding filler and the current intensity are decoupled here compared with other processes which work with a consumable electrode. The welder can therefore tune his power optimally to the welding task and only add as much welding filler as is currently required. This makes the method particularly suitable for welding root passes and for welding in predicaments. The advantages mentioned have led to the method being particularly well suited for welding aerospace equipment, components of nuclear technology, for the construction of chemical plants and equipment as well as of course for high-quality work by us on your vehicle and its parts.
Made to measure In the TIG process
The advantage of freedom from rust makes the TIG welding process, whether in aluminium or stainless-steel welding work, the first and only choice. With the TIG technology and our know-how it is easy to manufacture something like an intercooler for an Ascona C. The customer's demand was that the original appearance of the Ascona should not be falsified by an intercooler hanging under the apron.
In such everyday work as the production of charge air ducts, trouser pipes, downpipes, baffles in and on the body, etc., of course, the TIG process also comes into play.
Another advantage of our way of working is the fact that we build a welding gauge for custom-made products (such as for the front of a Bora 1.8T in the picture below) so that we can reproduce the part without having the vehicle in house.
It is best to convince yourself of our welding skills and to understand why customers from all over Germany and neighboring European countries come to us. Interested? Then you are welcome to contact us.